King Air Full Flight Simulators (FFS)
We provide state-of-the-art Full Flight Simulators (FFS) for the entire King Air series, covering the latest King Air generation as well as the many older models still in use.
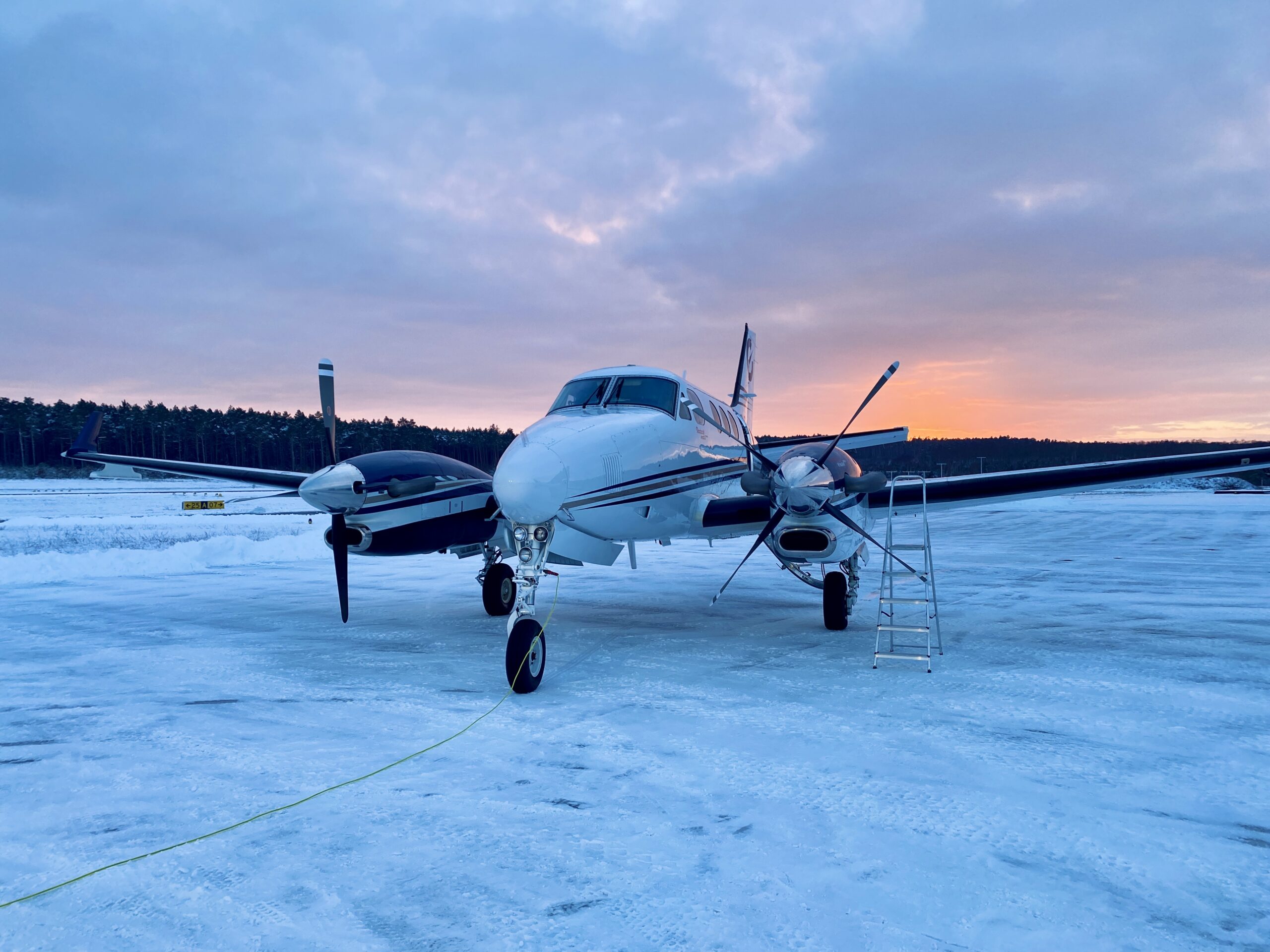
Beechcraft was founded in 1932 by Walter and Olive Ann Beech in Kansas, USA. From the beginning their aircraft were successful worldwide. The 1960s saw the launch of the Beechcraft King Air Series, one of the most versatile twin-turboprop series of all time. Its iterations cover everything from military roles to air ambulance to surveillance to business operators seeking a capable aircraft that can land where jets cannot. The King Air’s ability to operate from remote and unpaved runways has led to its use in extreme environments, from Alaska to South America.
Recent Milestones
- May 2025: Military Multi-Engine Training System (METS) selected for Canada’s Future Aircrew Training (FAcT)
- June 2025: Beechcraft King Air Multi-Mission Demonstration Aircraft (based on the most recent King Air 360) unveiled at the Paris Air show
Wide Array of Uses
Government agencies like NASA, NOAA, and INCAS use the King Air for weather research, environmental monitoring, and data-gathering missions, showcasing the aircraft’s adaptability and reliability in scientific fields.
The King Air is a common “first turbine” aircraft, which makes it especially relevant for training centers. Demand for simulators accordingly stays high, from King Air cockpit simulators all the way up to King Air Level D Simulators and King Air Full-Motion Simulators.
We provide state-of-the-art Full Flight Simulators (FFS) for the entire King Air series, covering the latest King Air generation as well as the many older models still in use. Our full flight simulators feature a training experience that is as close to the real aircraft as it gets, with peerless efficiency and availability.
Catering to the Differences
Many operators modify their aircraft with medical interiors, surveillance gear, custom avionics, etc. Indeed, King Airs are used in so many versions and configurations that almost no two individual aircraft are quite the same. Our clean, modular approach caters to these differences, and our RoRo simulators let training operators switch between configurations quickly and easily. Since so many King Airs are used in extreme environments, our simulators’ ability to present trainees with difficult terrains and weather conditions is another important benefit, as is our advanced icing simulation based on a range of scenarios.
The King Air FFS used by the INCAS weather research institute for their King Air C90-GTx is a case in point. We set it up so that INCAS can do its own test flights, gather their own aerodynamical test data and add it to the simulator. One of their requirements was that trainees be able to “see” the propellors, and the Visual System on all our King Air simulators has that capability.
Relentless Pursuit of Realism
We design and build our own panels in-house, so we can provide the highest level of detail precision. Further fidelity is assured by our use of original cockpit nose sections for full-flight simulators. It doesn’t stop on the ground either – we run our own flight tests to gather actual data on aircraft performance. This extends to propellor engine model development for turboprops like the King Air. Our pursuit of realism is relentless; for example, on the real Beechcraft crews can see the props, so we set up the Vision System so that trainees can see the simulated propellors.
Rockwell Collins offers a Pro Line 21 avionics upgrade for aircraft types including the Beechcraft King Air, and we can address that too. The AXIS IRIS Rehost Platform enables the integration of native aircraft software into flight training devices without the need for special hardware. The platform provides a fully emulated real-time environment running on COTS hardware with full ARINC610 support, to enable snapshots and extended malfunctions that would not be possible with OEM hardware. Its supports multiple software loads and airline options, easily switchable through the platform API. By using the unmodified aircraft ICD for data exchange and industry standard protocols (like ARINC429, AFDX and ARIN665), integration to an FTD is easily accomplished.
The AXIS Technical Monitor and Control System (TMCS) reflects our dedication to simulator availability. It drastically reduces maintenance time, and provides easy access to all information on simulator status, hardware, and IT components, plus an extensive knowledge base. Maintenance agility is outstanding, since TMCS can run on any mobile device via WiFi. Remote support by AXIS is also available through TMCS.